In October 2017, we headed for Turkey to learn about the production of organic cotton, from crops to garment manufacture.
In fact, it wasn’t our first business trip to Turkey. Since we created Picture in 2009, the bulk production of our lifestyle organic cotton products has been made by Seyfeli, in Izmir. So for almost 10 years we’ve been visiting the factory and office, 2 to 3 times per year, to work on product development and to follow up bulk production.
However, it was our first immersion in the whole process, starting from the crops. We were interested in knowing more about the supply chain. We all know what the final product looks like, but how about the components, dyeing, knitting and the human resources behind it?
Watch:
October 9th, 2017. After an awesome High Five Festival in Annecy, we are heading to Izmir for 5 days.
1st step: the cotton field.
Söke, Turkey.
When we talk about organic cotton, we first think about the cotton field.
But how are crops grown and how does organic agriculture differ from conventional agriculture?
Let’s look at 1 square meter of a cotton field. On a regular crop season, the traditional process will produce 500 grams of cotton whereas the organic growth process will get 200 grams. The use of toxic and persistent pesticides accelerates growth and increase production volume. However, this synthetic process has its limitations and will cause damages to soils and to people’s health.
During our visit, the farmer explained how the use of synthetic fertilizers weakens the soil overtime, neutralizing all the nutrient it naturally contains. 3 years of chemical agriculture require a 2 years break for the soil to recover its health… Additionally, since chemically fed soils weakens overtime, more water is required during the farming process.
Here is the difference between organic and synthetic farming:
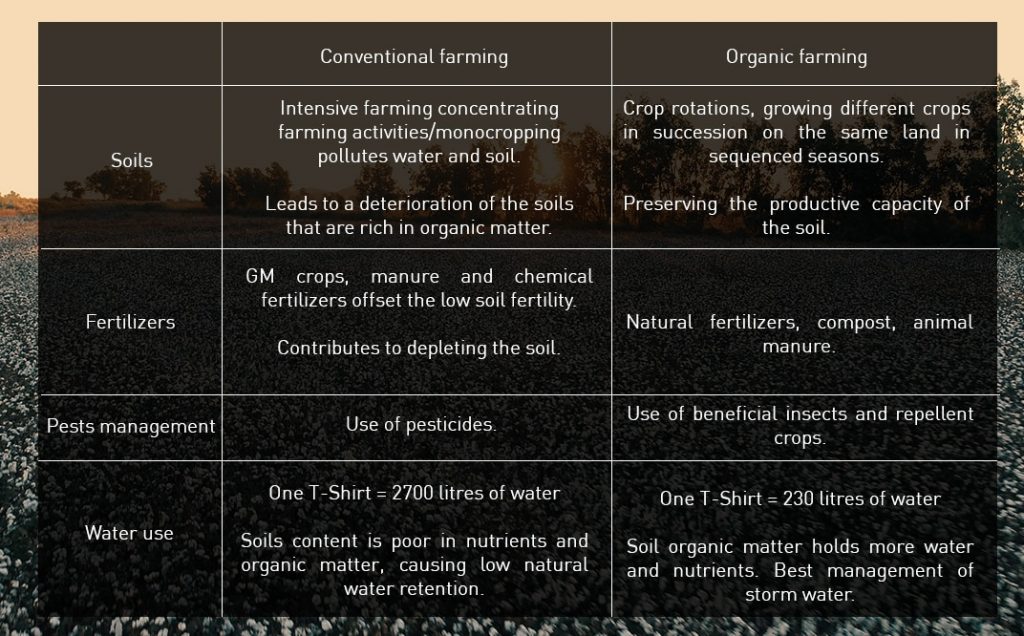
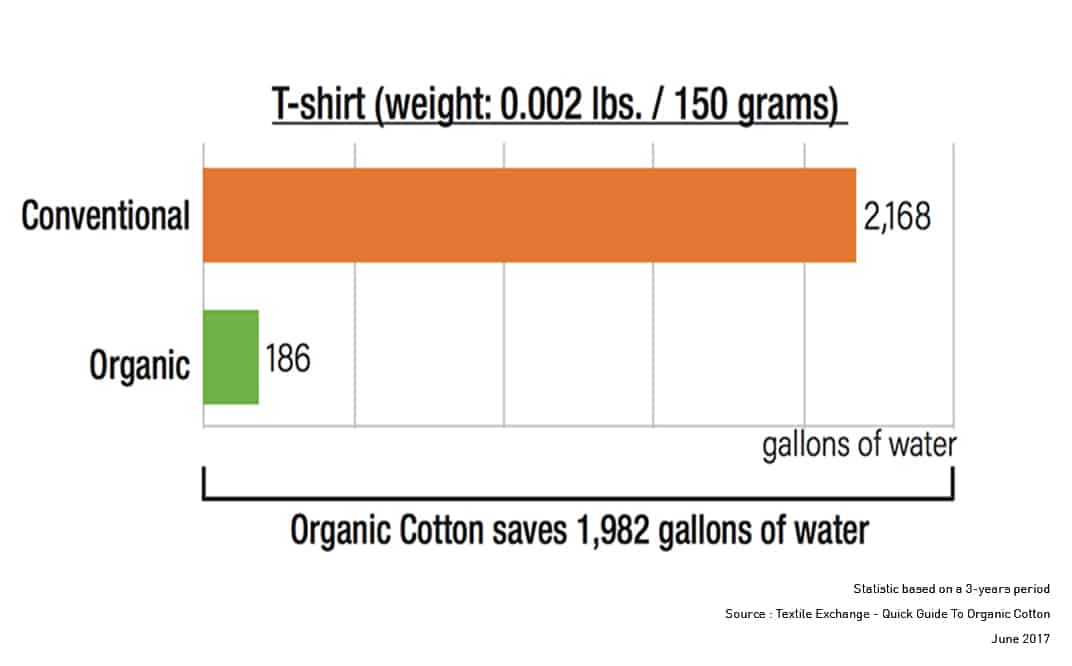
The comparisons drawn are remarkable and the environmental impact is clear. Organic agriculture can significantly reduce our impact on key environmental and socio-economic issues.
Recent findings (June 2017) by Textile Exchange include:
– Climate change and carbon emissions (CO2) (reduces 46%)
– Water eutrophication (Depletion) (reduces 26%)
– Soil salinity and acidification (reduces 70%)
– Water consumption (reduces 91%)
The exposure to toxic chemicals from synthetic pesticides and fertilizers used in conventional farming is associated with numerous health consequences. Volatile pesticides deplete air and soil quality, in addition to being harmful to both people and animals.
2nd step: Ginning.
Söke, Turkey.
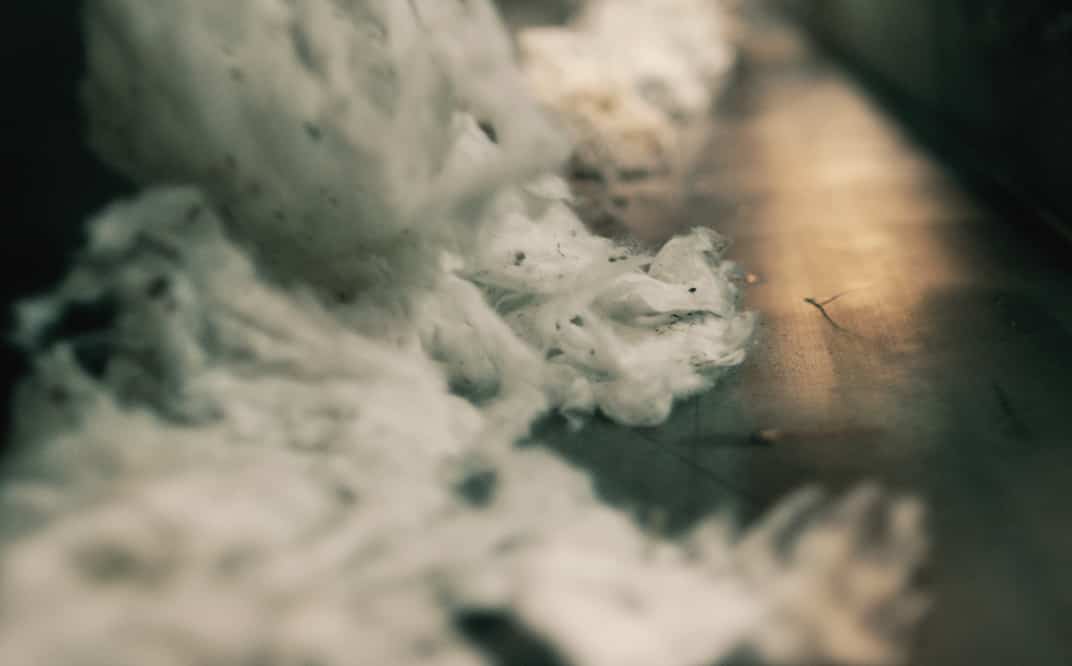
At nearly 10km from the cotton fields, the family-owned company Sökpam stocks the harvested cotton and then separates the fiber from the seed using the « ginning machine ». Sökpam owns the organic cotton fields we visited and carries out the ginning for other customers.
During the harvest season, trucks full of cotton flower come back from the fields, are weighed and then drop the cotton.
After ginning, the fiber is bundled and sent to the spinning process, while the seeds are prepared to be reused as crops, livestock food or cooking oil.
3th and 4th step: Spinning and knitting.
Torbali, Turkey.
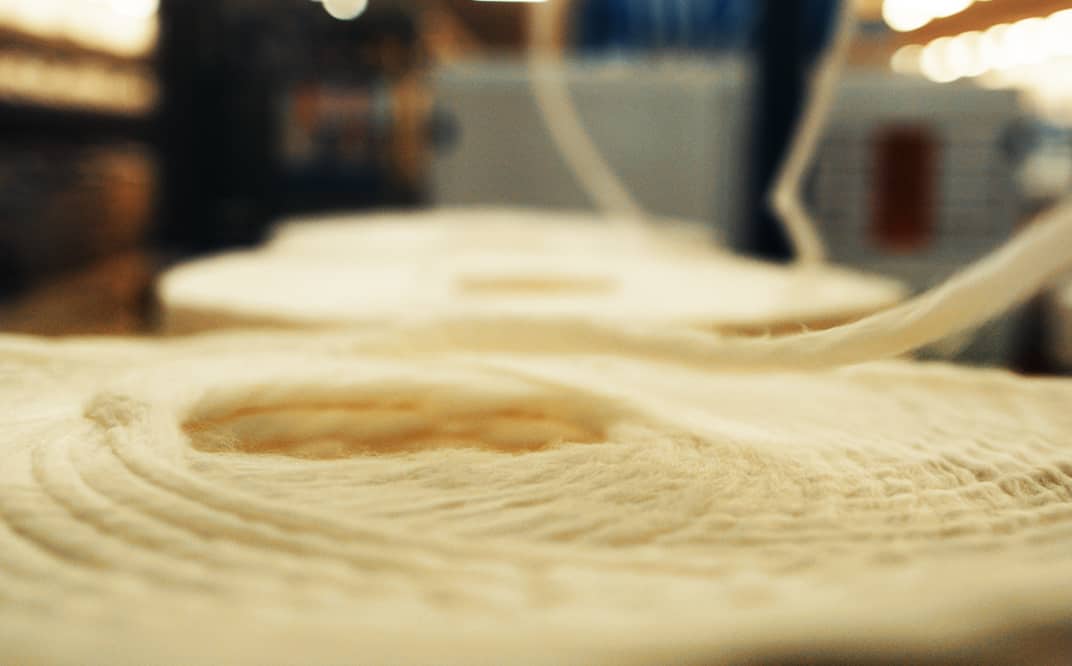
At 78km north of Söke, we get to Torbali, at Uçak Tekstil’s. This company performs the spinning and the knitting process. This is probably the most concrete yet intriguing step of the process!
How can rough and staple cotton fibers be transformed into a fine thread? We still had a hard time figuring it out, looking at the spinning machines…
The answer is: the twisting. The fibers are twisted together, roughly at first, shaping the cotton fibers into a cord. Then it is twisted again, in a stronger torque, to get a fine thread.
This is the reason why a thread will break easily when teared. The short-stapled fibers are simply spiraled together.
Above the spinning area are set multiple knitting machines. One machine uses 96 spools to produce the raw material.
5th step: Dyeing.
Torbali, Turkey.
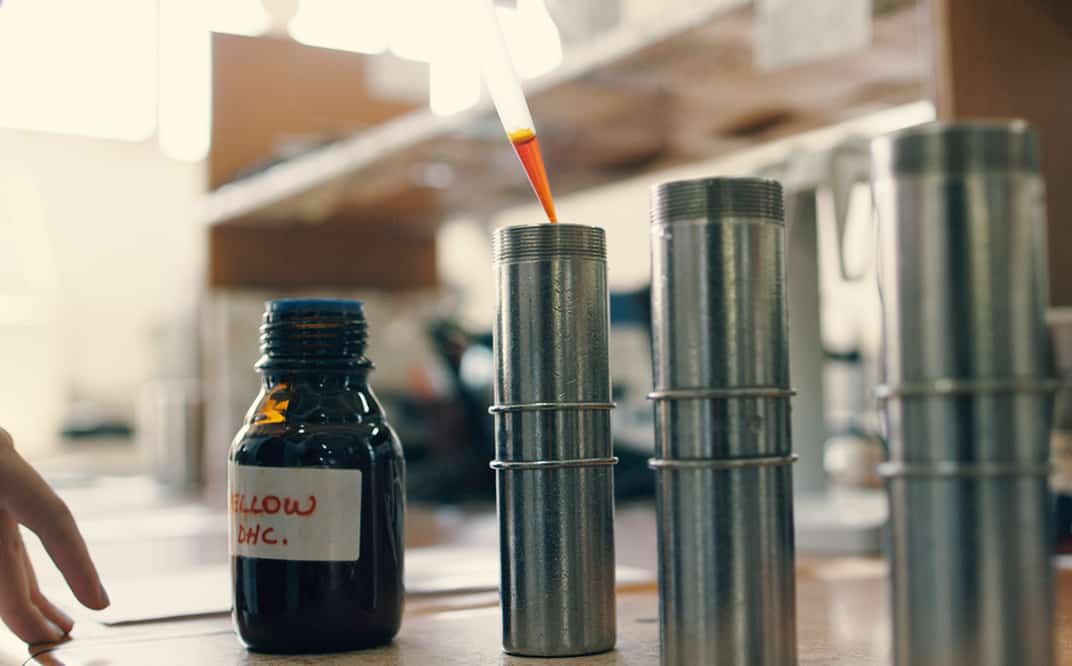
At 3km from the knitting site is Bati Basma, a textile dyes specialist. Here, the dyeing process is fully integrated, from the colour lab where chemists work in accordance with the Oeko-Tex 100 standard. The video tells so much more than these words, but imagine a giant washing machine in which the fabric will be dyed and a series of more of these machines to dry the coloured fabric and then test colour fastness.
The fabrics are dyed according customers’ requests. This is the reason why when we sketch our products using Illustrator, we pick Pantone colours references which the chemists will recreate in a dye.
Last step: Garment manufacturing.
Izmir, Turkey.
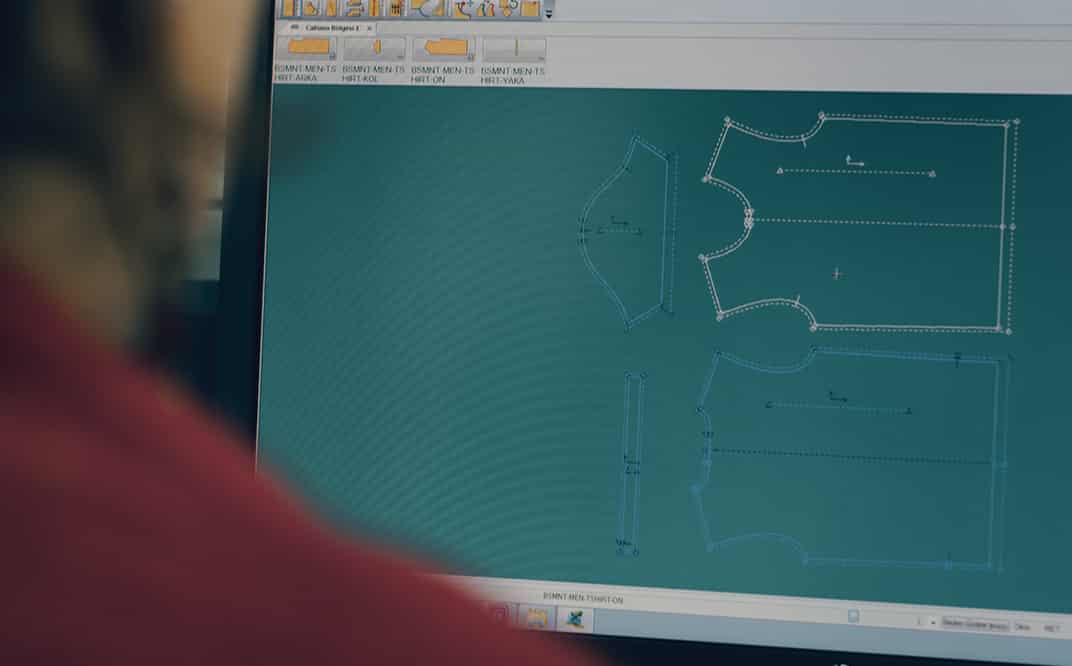
Located high in Izmir, with a scenic view on the Aegean Sea, we have been working together with Seyfeli garment factory on our products’ development for almost 10 years!
Patternmaking, water-based printing, embroidery and sewing are all done here, in order to get a finished product. They also offer prototyping, if needed.
Beyond garment manufacturing, the social and human aspects of the company struck our attention. Workspaces are immense, a cafeteria is opened at lunchtime for the employees and there is even a chill-out/recreational space with ping pong tables and an outdoor terrace.
Everyday at 3pm is « tea time »: everyone’s workspaces’ light automatically turn off and everyone gathers for a break.
But the best advantage working there is the free shuttle service. 2 shuttles take care of driving the employees to work and home. Multiple pick-up and drop-off locations fit everyone’s daily life.
Seray, the factory manager, brought two reasons to back up the service:
– The employee’s well being
– The urban road traffic in Izmir is oversaturated
As our visit comes to an end, our products are in the quality control stage, where they are ready to ship to stores and soon, to you.
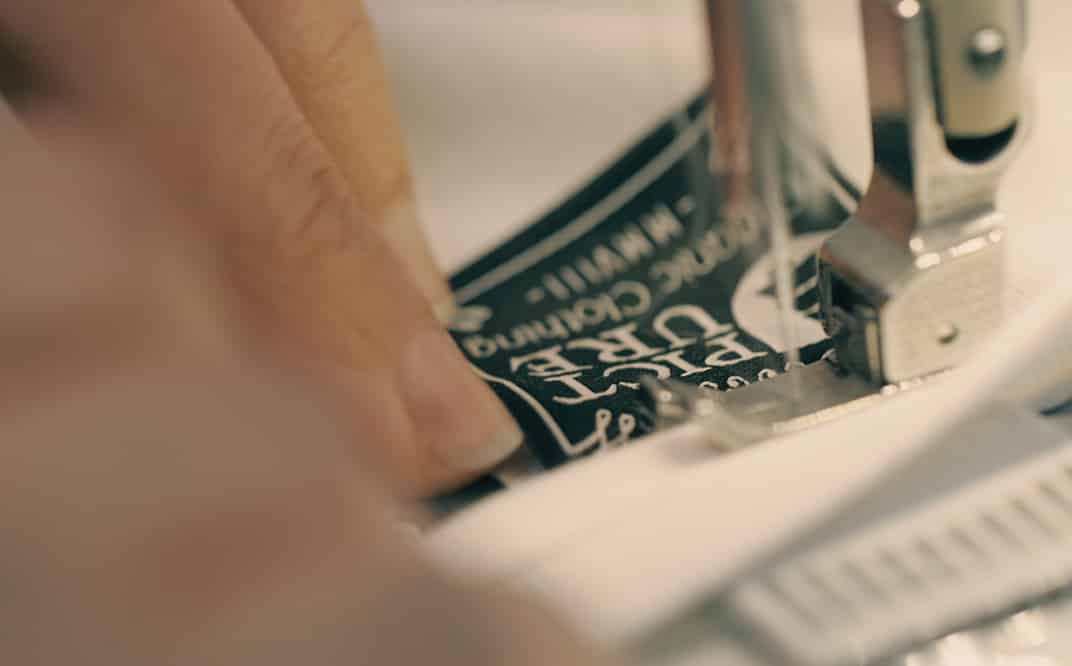
Our commitment to transparency is true, but our determination alone is not enough to guarantee social justice and the respect of the people we work with. That being said, we work with relevant professional organizations assisting the legislative process in the agricultural and chemical industries as well as social standards.
– GOTS and Organic Content Standard on organic cotton + social.
– Oeko-Tex 100 Standard 1 on the use of chemicals
– Fair Wear Foundation on the continuing improvement of working conditions.
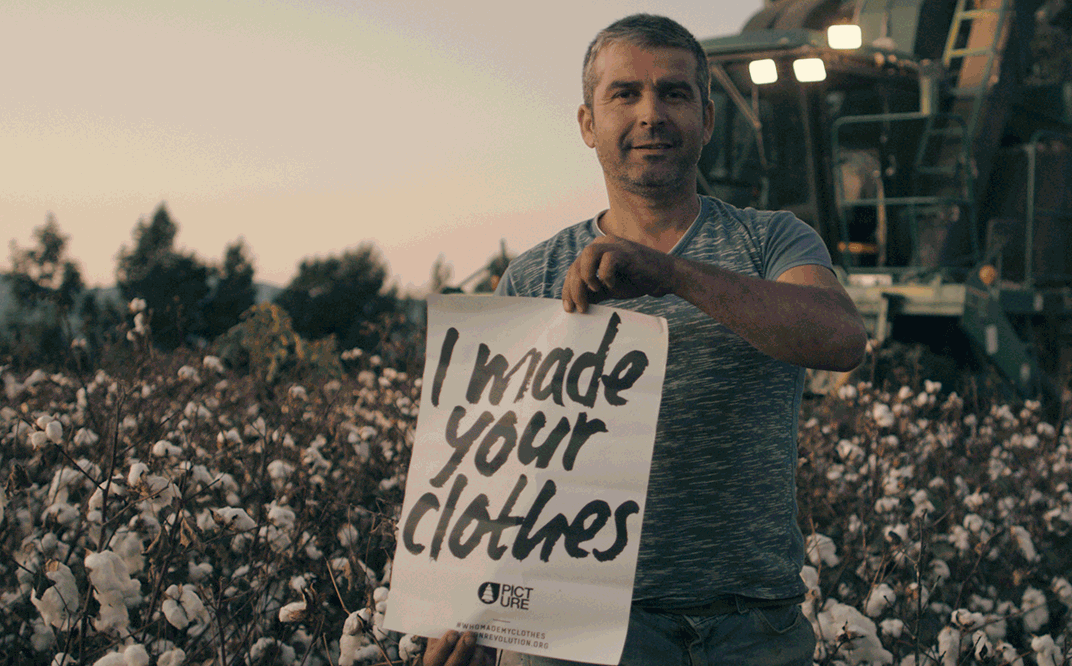